Dive Deep: Insights About Aluminum Casting Processes
Dive Deep: Insights About Aluminum Casting Processes
Blog Article
Explore the World of Aluminum Spreading: Expert Methods and secrets
In the realm of manufacturing, light weight aluminum casting stands as a critical process, critical for the production of a vast range of products. As we navigate with the globe of light weight aluminum casting, there exists a world of insider keys and techniques that can raise the quality of the final items and simplify the manufacturing procedure.
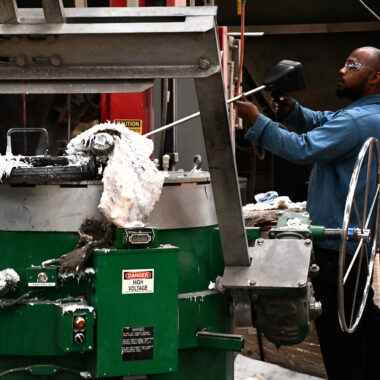
The Essentials of Light Weight Aluminum Spreading
Light weight aluminum spreading, a basic procedure in production, includes the putting of liquified light weight aluminum into a mold to attain wanted forms and structures. This versatile technique is extensively used across different markets as a result of aluminum's remarkable homes such as high strength-to-weight proportion, rust resistance, and thermal conductivity.
The procedure starts with the melting of light weight aluminum in a heater at temperatures exceeding 1220 ° F(660 ° C ) When the aluminum reaches its fluid state, it is poured right into a pre-designed mold and mildew tooth cavity. The mold, typically made from materials like steel or sand, establishes the final shape of the actors aluminum component.
After putting, the aluminum is left to strengthen and cool down within the mold - about aluminum casting. This cooling duration is vital as it determines the stability and high quality of the end product. As soon as strengthened, the mold and mildew is eliminated, disclosing the recently formed light weight aluminum spreading
Expert Tips for Effective Casting
To accomplish optimal outcomes in light weight aluminum casting, precise interest to information during the mold and mildew style stage is critical for making certain successful end results. Surveillance and regulating the steel temperature throughout the casting process can help avoid issues such as early solidification or porosity in the last item.
A well-prepared mold surface area can contribute to far better steel circulation, minimized disturbance, and enhanced surface coating on the actors component. By paying close focus to these expert tips, producers can boost the quality and efficiency of their light weight aluminum casting processes.
Advanced Techniques in Light Weight Aluminum Casting
Making use of cutting-edge methods and innovative approaches, the realm of light weight aluminum spreading has seen a substantial evolution in the direction of progressed strategies that push the limits of conventional techniques. One such method is vacuum casting, which entails producing a vacuum setting to get rid of air from the mold and mildew dental caries, leading to higher top quality and more detailed spreadings with reduced porosity. Furthermore, financial investment spreading, also referred to as lost-wax casting, is a refined technique that enables intricate forms and thin wall surfaces, resulting in accurate and thorough aluminum components.
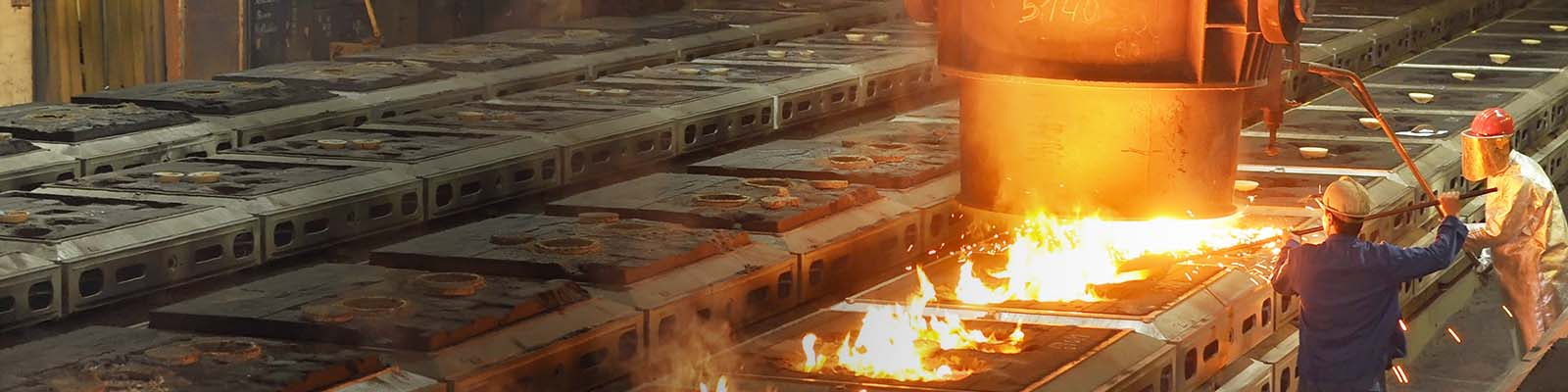
Moreover, progressed simulation software plays an important role in enhancing spreading designs and predicting prospective flaws, permitting for changes to be made before the actual casting procedure starts. By accepting these advanced methods, producers can raise their light weight aluminum casting capabilities to brand-new elevations, meeting the needs of modern-day sectors with accuracy and development.
Comprehending Various Casting Techniques
In the realm of production, a detailed understanding of various casting techniques is necessary for look at here accomplishing ideal cause metal manufacture procedures. Different spreading methods offer distinct advantages and are chosen based on elements such as the complexity of the design, manufacturing quantity, material demands, and price factors to consider. One of one of the most typical spreading techniques is sand spreading, where a mold and mildew is produced utilizing sand as the main product. Sand casting is flexible, cost-efficient, and suitable for producing large parts.
Another prominent casting technique is pass away spreading, which involves infusing molten metal right into a mold and mildew cavity under high stress. By understanding the subtleties of different spreading methods, suppliers can make educated decisions to maximize their production procedures and accomplish the wanted results.
Making The Most Of Performance in Spreading Operations
With a firm grip of the nuances of various casting approaches, suppliers can simplify their procedures to improve efficiency in metal manufacture procedures. Making the most of efficiency in casting operations calls for a methodical method that concentrates on optimizing every action of the casting process. One essential technique is to implement lean production principles to remove waste and enhance overall performance. By determining and removing bottlenecks in the assembly line, makers can enhance operations and minimize lead times.
Moreover, spending in innovative technology and equipment can significantly enhance effectiveness in casting procedures. Automated systems, robotics, and computer-aided style (CAD) software program can simplify procedures, decrease mistakes, and increase result. Additionally, training staff members on the current techniques and ideal practices can additionally add to making best use of performance in casting procedures.
Routine maintenance of equipment and tools is critical to minimize and prevent malfunctions downtime - about aluminum casting. Carrying out a proactive upkeep routine can assist identify potential concerns before they escalate, making certain smooth here operations and continuous production. In general, by prioritizing efficiency and continual improvement, producers can optimize their spreading procedures and stay affordable in the industry

Final Thought
In final thought, the globe of aluminum casting provides a broad range of chances for those looking to develop detailed and long lasting steel items. Recognizing the different spreading approaches and optimizing efficiency in procedures are key components to achieving high-grade results in light weight aluminum casting.
One such strategy is vacuum cleaner casting, which includes creating a vacuum cleaner setting to eliminate air from the mold and mildew tooth cavity, leading to higher top quality and more detailed castings with minimized porosity (about aluminum casting). Furthermore, investment spreading, likewise recognized as lost-wax casting, is Source a polished method that enables for slim wall surfaces and intricate shapes, resulting in thorough and specific aluminum parts
One of the most usual casting approaches is sand spreading, where a mold and mildew is developed making use of sand as the primary material.An additional popular casting approach is die spreading, which entails infusing liquified steel right into a mold and mildew cavity under high pressure. Comprehending the numerous casting methods and enhancing effectiveness in operations are vital elements to accomplishing top quality outcomes in light weight aluminum spreading.
Report this page